Centrifugal Polishing Machine Market
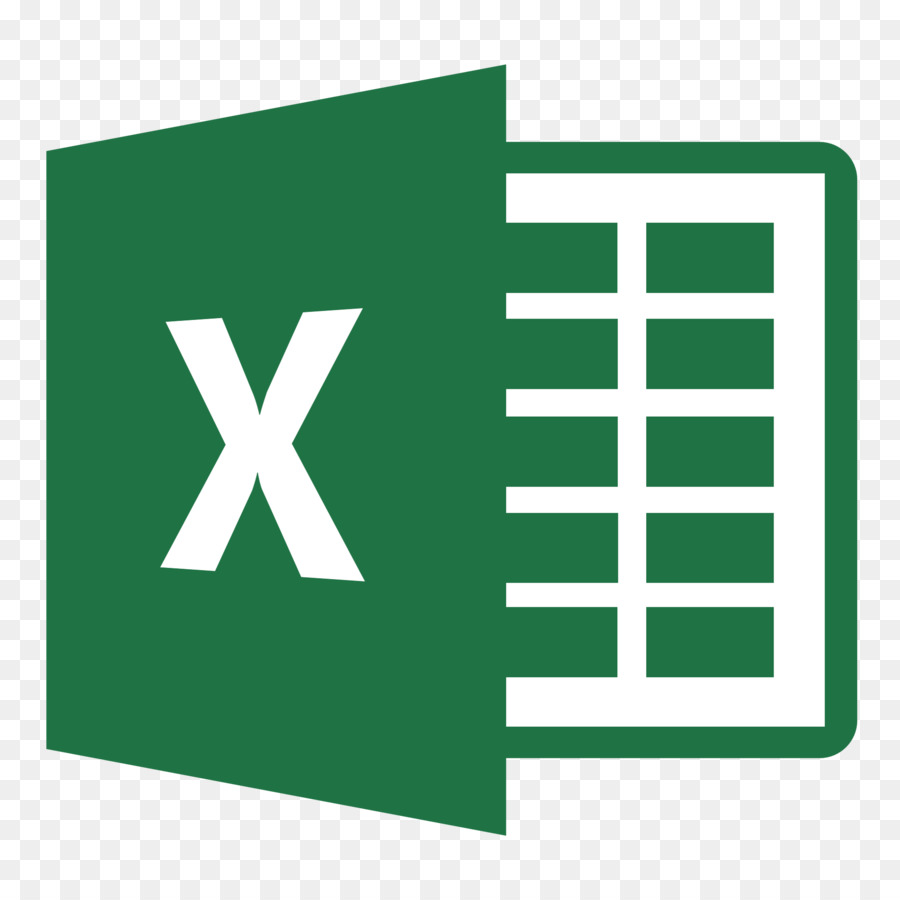
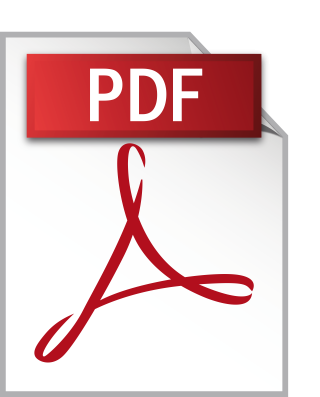
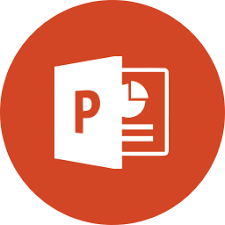
A centrifugal polishing machine is a surface finishing device that uses high-speed rotational forces to smooth, deburr, and polish materials. It operates by spinning workpieces inside a drum or chamber filled with abrasive media, applying centrifugal force for efficient and uniform polishing. This method is commonly used for improving the surface quality of metal, plastic, and other materials.
The centrifugal polishing machine market is driven by the growing demand for high-precision finishing in industries such as aerospace, automotive, and medical devices. The rise of automation and smart manufacturing is increasing adoption as companies seek efficient and consistent polishing solutions. Challenges include high initial investment costs and the need for skilled operators to manage advanced machinery. Opportunities lie in the integration of IoT, AI-driven process optimization, and the expanding use of 3D printing, which requires effective post-processing solutions.
The growing demand for high-precision finishing in manufacturing industries is driving the centrifugal polishing machine market. Many industries, including aerospace, automotive, medical devices, and electronics, require components with smooth surfaces and precise dimensions to ensure optimal performance and durability. Centrifugal polishing machines offer high-efficiency finishing by reducing surface roughness and eliminating imperfections, making them essential in industries where quality and precision are critical. As manufacturing processes become more advanced, the need for automated and efficient finishing solutions continues to rise, leading to increased adoption of centrifugal polishing machines.
The expansion of the automotive industry is contributing to the increasing demand for centrifugal polishing machines. Automotive manufacturers require high-quality surface finishing for engine components, transmission parts, and decorative elements to enhance both performance and aesthetics. The growing trend toward electric vehicles has further increased the need for precision finishing in battery components and lightweight materials like aluminum and composites. As vehicle production volumes continue to rise globally, manufacturers seek automated and cost-effective finishing solutions to improve efficiency, reduce labor costs, and maintain consistent product quality. The adoption of centrifugal polishing machines helps automotive companies achieve these goals while meeting strict industry standards.
The medical device industry is fueling the demand for centrifugal polishing machines due to strict hygiene and quality requirements. Surgical instruments, orthopedic implants, and dental devices must have extremely smooth surfaces to prevent contamination and ensure biocompatibility. Polishing processes play a crucial role in removing surface irregularities that could harbor bacteria or cause discomfort to patients. With advancements in medical technology and an increasing number of surgical procedures worldwide, manufacturers are investing in high-precision polishing solutions to comply with stringent regulatory requirements and improve the longevity and performance of medical devices.
The rise of automation and smart manufacturing is driving the adoption of centrifugal polishing machines. Many industries are shifting toward automated production lines to increase efficiency and reduce reliance on manual labor. Centrifugal polishing machines integrate seamlessly into automated workflows, offering consistent and repeatable finishing results with minimal operator intervention. The introduction of Industry 4.0 technologies, including IoT-enabled monitoring and robotic integration, has further enhanced the efficiency of these machines. As industries seek to improve productivity and reduce processing time, the demand for advanced polishing solutions continues to grow, supporting market expansion.
The increasing use of 3D printing in manufacturing is creating new opportunities for centrifugal polishing machines. Additive manufacturing produces complex parts with intricate geometries, but the printed components often require post-processing to achieve the desired surface finish. Centrifugal polishing machines provide an effective solution for smoothing and refining 3D-printed parts, ensuring they meet industry standards for functionality and appearance. As 3D printing adoption grows across sectors such as aerospace, healthcare, and consumer goods, the need for efficient post-processing technologies is expected to drive the demand for centrifugal polishing machines.
The global centrifugal polishing machine market faces challenges related to high initial costs, which can limit adoption, especially among small and medium-sized enterprises. The complexity of operation and maintenance requires skilled labor, creating difficulties in regions with a shortage of trained professionals. Variability in raw material prices affects manufacturing costs, leading to pricing fluctuations that can impact market stability. Strict environmental regulations related to industrial waste and emissions force manufacturers to invest in eco-friendly solutions, increasing operational costs. Supply chain disruptions, including delays in sourcing critical components, affect production timelines and delivery schedules. The market also encounters competition from alternative surface finishing technologies, such as vibratory and ultrasonic polishing, which offer different cost and efficiency benefits. Economic uncertainties, such as inflation and currency fluctuations, impact investment decisions and overall demand for industrial machinery. Rapid technological advancements require continuous innovation, and companies that fail to keep up risk losing market relevance. Customization demands from different industries add complexity to production processes, increasing costs and time-to-market challenges. Market penetration in developing regions is hindered by a lack of awareness and limited infrastructure, making it difficult for manufacturers to expand their presence in these areas.
The growing adoption of automation and smart manufacturing technologies presents a significant opportunity for the centrifugal polishing machine market. Industries are increasingly investing in automated systems to improve efficiency, reduce labor costs, and maintain high-quality production standards. Centrifugal polishing machines with advanced features such as programmable controls, IoT connectivity, and real-time monitoring are gaining traction as manufacturers seek intelligent solutions for surface finishing. The integration of robotics and AI-driven process optimization allows for greater precision and consistency in polishing operations, catering to industries such as aerospace, automotive, and medical devices. As factories transition toward Industry 4.0 and digital manufacturing, the demand for highly efficient and technologically advanced polishing machines is expected to increase, creating new growth opportunities for market players.
Product Type
The automatic segment in the centrifugal polishing machine market is experiencing strong growth due to the increasing demand for high-efficiency and labor-saving polishing solutions. Industries such as aerospace, automotive, and medical devices require consistent and precise surface finishing, which automatic machines provide with minimal human intervention. These machines are equipped with advanced features such as programmable controls, real-time monitoring, and robotic integration, allowing for improved accuracy and productivity. The growing adoption of smart manufacturing and Industry 4.0 technologies is further driving demand for automatic centrifugal polishing machines. This segment is the dominating category in the market, as large-scale manufacturers prefer automated solutions to enhance efficiency, reduce costs, and maintain product quality.
The semi-automatic segment holds a significant share in the centrifugal polishing machine market, particularly among small and medium-sized enterprises that require a balance between automation and manual control. These machines offer flexibility, allowing operators to adjust polishing parameters based on specific requirements while still benefiting from automated processes that reduce manual labor. Industries with lower production volumes or specialized finishing needs prefer semi-automatic machines due to their cost-effectiveness and adaptability. This segment is the fastest-growing category, driven by increasing demand from emerging markets and businesses looking for an affordable transition from manual to automated polishing solutions. As industries continue to modernize, the adoption of semi-automatic machines is expected to rise, providing growth opportunities for manufacturers catering to diverse customer needs.
Application
The use of centrifugal polishing machines in car parts manufacturing plays a crucial role in enhancing the durability and appearance of automotive components. These machines are widely used for polishing metal and alloy parts, such as engine components, gears, and brake systems, ensuring a smooth surface finish and reducing friction. The automotive industry demands high precision and quality, making polishing essential for both aesthetic and functional improvements. The growing demand for electric vehicles and lightweight materials further increases the need for efficient surface finishing solutions.
In the production of electronic product casing, centrifugal polishing machines are essential for achieving smooth and refined surfaces. Consumer electronics, such as smartphones, laptops, and home appliances, require polished casings to enhance visual appeal and durability. The rapid advancement in technology and increasing demand for compact and sleek designs drive the need for high-quality finishing processes. Manufacturers focus on improving surface uniformity while maintaining efficiency in mass production. The shift toward premium electronic products with superior surface quality fuels the adoption of advanced polishing techniques.
Glassware production benefits significantly from centrifugal polishing machines, as they help create smooth and glossy surfaces for decorative and functional glass products. These machines are used to refine the edges and surfaces of glass items such as tableware, laboratory equipment, and optical lenses. High precision is required to ensure clarity and eliminate imperfections that could affect product performance. The increasing demand for high-end glass products in industries such as hospitality, healthcare, and consumer goods contributes to the steady adoption of polishing solutions in this segment.
Various other industries also rely on centrifugal polishing machines for surface finishing applications. Sectors such as jewelry, medical devices, and aerospace require precise polishing to meet strict quality standards. In jewelry manufacturing, polishing enhances the shine and smoothness of metal pieces, improving their visual appeal. The medical industry depends on polished surgical instruments and implants to ensure safety and hygiene. Aerospace components require a flawless finish to maintain structural integrity and performance. The demand for customized polishing solutions in different industries continues to grow as manufacturers seek efficient ways to improve product quality.
North America experiences steady growth in the centrifugal polishing machine market due to advanced manufacturing industries, particularly in aerospace, automotive, and medical sectors. High demand for precision-engineered components drives the need for efficient polishing solutions, while strict environmental regulations push companies to adopt sustainable technologies. The region has strong research and development capabilities, encouraging innovation in surface finishing techniques. However, high labor costs and supply chain disruptions challenge market expansion. Established players focus on automation and smart technologies to enhance machine efficiency and reduce operational costs.
Europe benefits from a well-developed industrial base, with major countries like Germany, France, and the United Kingdom leading in automotive, aerospace, and heavy machinery manufacturing. The presence of stringent quality and safety standards in industrial processes drives the adoption of high-performance polishing equipment. The shift toward Industry 4.0 and smart manufacturing accelerates demand for automated and energy-efficient machines. However, high initial investment costs and economic fluctuations impact market growth. Companies in the region emphasize sustainability, leading to the development of eco-friendly and energy-efficient polishing systems to comply with strict environmental policies.
Asia Pacific is the fastest-growing market, driven by rapid industrialization and increasing manufacturing activities in China, Japan, South Korea, and India. The booming automotive, electronics, and metalworking industries create strong demand for centrifugal polishing machines. Favorable government policies supporting industrial automation and foreign investments in manufacturing further boost market expansion. However, the presence of low-cost alternatives and unorganized local manufacturers creates pricing pressure on global players. The rising adoption of advanced polishing technologies, along with growing awareness of quality standards, fuels market growth despite challenges related to fluctuating raw material prices and labor shortages.
Latin America sees gradual growth as industrial sectors in Brazil, Mexico, and Argentina expand. The automotive and aerospace industries are key drivers, along with increasing foreign investments in manufacturing. However, economic instability, political uncertainties, and a lack of skilled labor hinder widespread adoption. The presence of price-sensitive customers encourages manufacturers to offer cost-effective and durable polishing solutions. Companies focus on enhancing local production capabilities and forming strategic partnerships to strengthen their market position in the region.
The Middle East & Africa region has emerging demand for centrifugal polishing machines, driven by growth in construction, oil and gas, and industrial manufacturing. Infrastructure development projects increase the need for precision-machined components, fueling demand for efficient surface finishing solutions. However, limited industrial automation, lower awareness of advanced polishing techniques, and economic challenges restrict market growth. Manufacturers explore opportunities by partnering with local distributors and investing in training programs to improve technology adoption in the region. The market is gradually expanding as industries modernize and seek high-quality surface finishing solutions to meet international standards.