Tapping Equipment Market
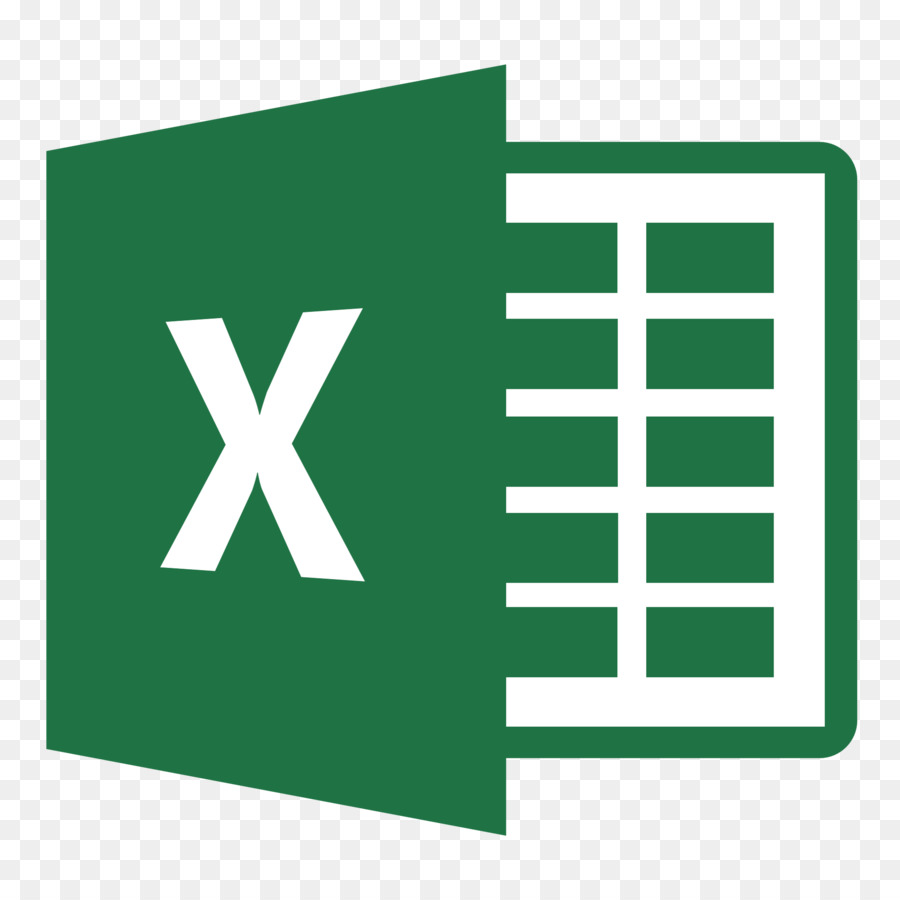
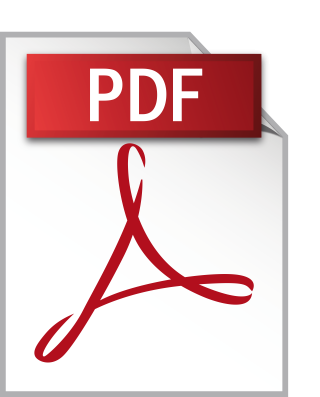
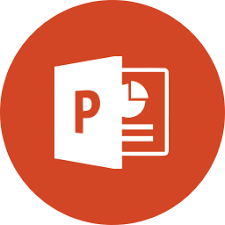
Tapping equipment is a machine or tool used to create internal threads in metal, plastic, or other materials by cutting or forming threads inside pre-drilled holes. It ensures precise and consistent threading for components like bolts, nuts, and fittings, which are essential in manufacturing and assembly processes. The equipment operates manually or automatically, depending on the production requirements and material type.
The tapping equipment market is driven by the growing demand for precision machining, industrial automation, and advancements in cutting tool technology. Challenges include high competition, the need for continuous innovation, and the rising cost of advanced machinery. Opportunities exist in customized tapping solutions, expansion into emerging markets, and the integration of smart manufacturing technologies. The shift toward sustainable production and digitalization further enhances market potential.
The increasing demand for precision machining in various industries is a major factor driving the growth of the tapping equipment market. Sectors such as automotive, aerospace, electronics, and industrial manufacturing require high-precision threading for assembling components with accuracy and efficiency. The need for high-quality tapped holes in materials like metal, plastic, and composites has led manufacturers to adopt advanced tapping machines that ensure consistency and reliability in production. As industries continue to emphasize quality control and precision engineering, the adoption of automated and CNC-based tapping solutions is expected to rise.
The rapid growth of industrial automation and smart manufacturing technologies has significantly influenced the tapping equipment market. Factories and production units are increasingly integrating automated tapping systems into their workflows to enhance efficiency and reduce labor dependency. CNC and robotic tapping machines provide faster operations, reduce human error, and improve overall productivity. The transition toward Industry 4.0, where interconnected systems enable real-time monitoring and process optimization, has further increased the demand for intelligent tapping solutions with programmable controls and remote operation capabilities. Manufacturers investing in automation-driven tapping equipment gain a competitive edge by reducing production costs and increasing throughput.
The expansion of the automotive and aerospace industries has fueled the demand for advanced tapping equipment capable of handling complex materials and designs. These industries require high-strength threaded components to ensure safety and performance in critical applications. The shift toward lightweight materials, such as aluminum and carbon fiber composites, has driven the need for specialized tapping solutions that can maintain precision without compromising material integrity. With the rising production of electric vehicles and next-generation aircraft, tapping equipment manufacturers must develop innovative threading technologies to meet evolving industry requirements.
The rising adoption of tapping equipment in small and medium-sized enterprises (SMEs) has contributed to market expansion. SMEs in metalworking, fabrication, and general manufacturing seek cost-effective yet efficient tapping solutions to improve operational capabilities. The availability of compact and user-friendly tapping machines has allowed smaller businesses to enhance production quality while maintaining affordability. As SMEs continue to modernize their manufacturing processes, the demand for semi-automatic and entry-level CNC tapping machines is expected to grow, creating opportunities for equipment providers to cater to this segment.
The development of high-performance cutting tools and tapping technologies has accelerated market growth by improving efficiency and extending tool life. Advancements in tap coatings, materials, and geometries enable better performance in challenging applications, such as tapping hardened steel, titanium, and heat-resistant alloys. High-speed tapping machines with adaptive feed control and lubrication systems have enhanced threading capabilities, reducing wear and increasing tool longevity. Continuous research and development efforts by manufacturers to introduce innovative cutting solutions have strengthened the adoption of tapping equipment in industries with demanding machining requirements.
The increasing focus on energy efficiency and sustainability in manufacturing has led to the development of eco-friendly tapping equipment. Companies are seeking energy-efficient machines that reduce power consumption while maintaining high productivity. Advanced servo-driven tapping machines and optimized lubrication systems contribute to lower environmental impact by minimizing waste and improving operational efficiency. Government regulations and corporate sustainability initiatives further encourage the adoption of tapping solutions that align with green manufacturing practices. Equipment manufacturers that prioritize energy-efficient designs and sustainable materials position themselves favorably in an evolving market landscape.
The tapping equipment market faces challenges related to high initial investment costs, making it difficult for small and medium-sized manufacturers to adopt advanced machinery. The need for precision in threading applications requires continuous maintenance and calibration, increasing operational expenses for businesses. Variability in material hardness and composition can lead to tool wear and frequent replacements, adding to production costs and downtime. Skilled labor shortages further impact market growth, as operating and maintaining tapping equipment require technical expertise that is not always readily available. The rise of automated and CNC machining solutions is changing industry standards, forcing traditional manufacturers to invest in technology upgrades to stay competitive. Supply chain disruptions and fluctuating raw material prices also create instability in production and pricing strategies. Compliance with stringent safety and quality regulations across different regions adds complexity to manufacturing and distribution, leading to increased costs and longer approval times for new products. Market competition from low-cost alternatives and counterfeit products affects brand reputation and profitability, especially in price-sensitive regions.
The increasing demand for customized tapping solutions presents a significant opportunity for manufacturers in the tapping equipment market. Industries require specialized tapping machines that can accommodate different materials, thread sizes, and production volumes. Companies that offer modular or adaptable tapping systems with configurable settings can attract businesses looking for flexible and efficient solutions. The ability to provide customized automation options, such as integration with robotic arms or smart control systems, enhances the appeal of tapping equipment for manufacturers seeking tailored production processes.
The expansion of the tapping equipment market in emerging economies creates a strong growth potential for manufacturers and suppliers. Rapid industrialization in countries across Asia, Latin America, and Africa has led to increased investment in manufacturing infrastructure, particularly in automotive, aerospace, and general engineering sectors. Small and medium-sized enterprises in these regions are adopting modern machining solutions to improve productivity and meet global quality standards. Establishing local production facilities, distribution networks, and service centers in these regions can help companies capitalize on the growing demand for tapping equipment.
The rising trend of additive manufacturing and hybrid machining presents opportunities for tapping equipment manufacturers to develop solutions compatible with new production methods. 3D printing and advanced metalworking techniques require precise post-processing, including tapping, to ensure functional and high-quality components. Companies that innovate tapping solutions specifically designed for hybrid manufacturing environments can cater to industries adopting these technologies. The development of tapping equipment that integrates seamlessly with CNC machining centers and additive manufacturing workflows provides an advantage for manufacturers seeking comprehensive production capabilities.
The shift toward digitalization and smart manufacturing opens avenues for tapping equipment manufacturers to introduce intelligent and connected machines. Smart tapping machines equipped with sensors, IoT-enabled monitoring, and data analytics can improve operational efficiency by detecting tool wear, optimizing cycle times, and predicting maintenance needs. The demand for real-time production insights and automated troubleshooting in industrial settings increases the appeal of tapping equipment with advanced digital features. Companies that focus on integrating artificial intelligence and machine learning for process optimization can differentiate themselves in the market and attract industries embracing Industry 4.0 initiatives.
The growing emphasis on sustainable manufacturing practices creates opportunities for tapping equipment producers to develop energy-efficient and environmentally friendly solutions. Industries are seeking machines that consume less power, reduce material waste, and operate with minimal coolant usage. Innovations in dry tapping, high-efficiency servo motors, and recyclable machine components can meet the demand for greener production methods. Companies that align their tapping equipment with sustainability goals and regulatory requirements can appeal to businesses prioritizing eco-conscious manufacturing while gaining a competitive edge in the market.
Product Type
Manual tapping equipment is widely used in small-scale industries and workshops where precision threading is required without the need for automation. These machines are cost-effective and easy to operate, making them a preferred choice for applications with low production volumes. The flexibility of manual tapping equipment allows operators to handle a variety of materials, including metals and plastics, with greater control over the threading process. Maintenance and repair costs are relatively low compared to automated systems, making them suitable for businesses with budget constraints. Despite their advantages, manual machines require skilled labor and are time-consuming, which limits their efficiency in large-scale manufacturing operations.
Automatic tapping equipment is the dominating and fastest-growing segment in the market due to its ability to increase productivity and reduce human errors. These machines are integrated with advanced features such as CNC control, automated threading, and high-speed operation, making them ideal for industries with high production demands. The adoption of automatic tapping equipment is rising in sectors like automotive, aerospace, and industrial manufacturing, where precision and consistency are critical. Reduced labor dependency and faster cycle times contribute to cost savings for businesses, despite the higher initial investment. Continuous advancements in automation technology and smart manufacturing are further driving the demand for automatic tapping machines, making them the preferred choice for large-scale production facilities.
Application
The production of bolts relies heavily on precise and efficient tapping equipment to create high-quality threaded fasteners used in construction, automotive, and industrial applications. Bolts require accurate threading to ensure secure fastening and durability under various stress conditions. Advanced tapping machines with high-speed operations and automated controls help manufacturers achieve uniform thread quality, reducing defects and improving production efficiency. As industries demand stronger and more specialized bolts, tapping equipment must evolve to handle different materials, such as high-strength steel and corrosion-resistant alloys, ensuring that fasteners meet stringent performance standards.
The manufacturing of nuts depends on reliable tapping processes to produce threads that align perfectly with corresponding bolts and fasteners. Nuts must have precise internal threading to maintain a strong grip and prevent loosening under mechanical stress. Tapping equipment designed for nut production must offer high-speed operation, consistent threading accuracy, and minimal material wastage. The increasing use of self-locking and high-performance nuts in aerospace, automotive, and heavy machinery applications has driven the need for advanced tapping solutions. Manufacturers are focusing on automated and multi-spindle tapping machines to boost productivity and meet the growing demand for high-quality nuts in various industries.
The production of pipe fittings requires specialized tapping equipment to create threaded connections for plumbing, oil and gas, and industrial fluid transport systems. Threaded pipe fittings, such as couplings, elbows, and tees, must have precise internal and external threads to ensure leak-proof connections. Tapping machines used in this segment must accommodate different pipe sizes and materials, including stainless steel, brass, and PVC. The growing adoption of threaded fittings in infrastructure projects and industrial applications has increased the need for high-efficiency tapping equipment capable of handling mass production while maintaining precision and reliability.
The bearing industry relies on tapping equipment to create threaded holes for securing bearing housings and related components in machinery and automotive systems. Bearings must be assembled with precision to minimize friction and ensure smooth rotation in mechanical applications. High-precision tapping machines are essential to producing consistent and accurate threads that allow secure attachment and proper alignment of bearing units. The increasing demand for high-performance bearings in robotics, aerospace, and electric vehicles has led manufacturers to adopt advanced tapping technologies that enhance productivity and meet stringent quality requirements.
The others segment includes various applications where threaded components are essential, such as medical devices, consumer electronics, and industrial machinery. Medical implants, such as orthopedic screws, require micro-tapping equipment to produce fine and precise threads for secure bone fixation. Electronic enclosures and casings often require threading for assembly and durability in harsh environments. Industrial equipment, such as pumps and valves, also depend on tapped components for secure fittings and operational efficiency. The growing demand for precision-engineered products across different industries has created opportunities for tapping equipment manufacturers to develop specialized solutions tailored to unique application requirements.
North America has a well-established tapping equipment market driven by strong demand from the automotive, aerospace, and industrial manufacturing sectors. The presence of advanced production facilities and a focus on automation have increased the adoption of high-precision tapping machines. Companies in the region are investing in research and development to enhance tool performance and efficiency. However, rising labor costs and the need for skilled workers pose challenges for manufacturers. The market is competitive, with several players offering innovative solutions to meet the evolving needs of industries. Strict regulations related to manufacturing standards and workplace safety also influence equipment design and adoption.
Europe has a growing tapping equipment market, supported by the expansion of the automotive and machinery industries. Countries like Germany, France, and Italy have a strong presence of precision engineering companies that require high-quality threading solutions. The region's focus on sustainability and energy efficiency has led to increased demand for eco-friendly manufacturing processes, encouraging the adoption of advanced tapping equipment. High production costs and stringent environmental regulations create challenges for manufacturers. The presence of well-established companies and the adoption of Industry 4.0 technologies are shaping the competitive landscape. Import and export regulations across different countries affect supply chains and product availability.
Asia Pacific is the fastest-growing market for tapping equipment, driven by rapid industrialization and the expansion of manufacturing hubs in China, India, Japan, and South Korea. The increasing demand for consumer electronics, automobiles, and construction materials has fueled the need for efficient tapping solutions. The availability of low-cost labor and raw materials has made the region attractive for global manufacturers. However, competition from local players offering affordable alternatives challenges international brands. The shift towards automation and smart manufacturing is creating opportunities for advanced tapping equipment. Government initiatives to promote domestic manufacturing are further driving market growth. The presence of counterfeit products and inconsistent quality standards remains a concern for industry players.
Latin America is experiencing steady growth in the tapping equipment market, primarily due to the expansion of the automotive and metalworking industries. Brazil and Mexico are key markets, benefiting from foreign investments in industrial production. The demand for durable and cost-effective tapping solutions is rising as industries seek to improve production efficiency. However, economic instability and fluctuating currency values impact equipment pricing and investment decisions. The region has a growing number of small and medium-sized manufacturers looking for affordable solutions, which presents opportunities for cost-competitive products. Limited access to advanced technology and skilled labor remains a challenge for market expansion.
The Middle East & Africa market for tapping equipment is developing, with growth driven by the construction, oil and gas, and infrastructure sectors. The demand for high-quality industrial components has led to increased investment in precision manufacturing tools. Countries like the UAE and Saudi Arabia are focusing on industrial diversification, boosting the need for modern tapping solutions. Limited local production capabilities create a dependency on imports, which can result in higher costs and longer lead times. The adoption of automation is slower compared to other regions due to budget constraints and a lack of technical expertise. Government initiatives to strengthen domestic industries and infrastructure development projects are expected to support market growth.